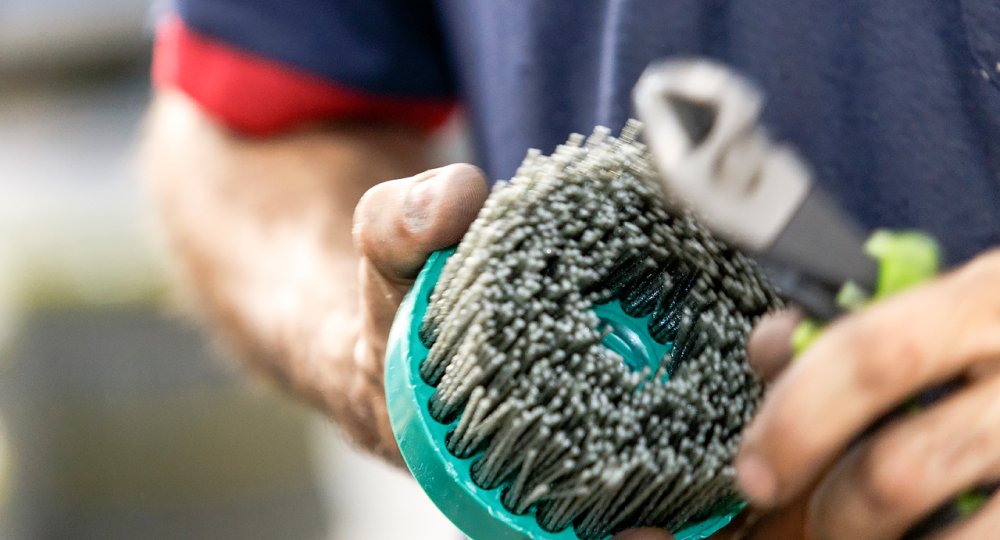
Lean manufacturing è una metodologia che enfatizza l’uso efficiente delle risorse, la riduzione degli sprechi e il miglioramento della qualità. Ha le sue radici nel Toyota Production System (TPS) sviluppato da Taiichi Ohno e Eiji Toyoda in Giappone negli anni ’50. Il TPS è stato sviluppato per migliorare la produttività e ridurre gli sprechi nelle operazioni di produzione Toyota, e da allora è stato adottato da molte altre aziende Intorno al mondo.
Cos’è la Lean Manufacturing?
Lean manufacturing è un sistema di produzione che mira a ridurre al minimo gli sprechi, ridurre i costi e aumentare l’efficienza. L’obiettivo principale della lean manufacturing è quello di creare valore per i clienti riducendo al minimo le risorse utilizzate nel processo produttivo. Ciò si ottiene attraverso l’identificazione e l’eliminazione degli sprechi, tra cui sovrapproduzione, attese, difetti, inventario in eccesso, movimenti non necessari, elaborazione eccessiva e talento inutilizzato.
Vantaggi della Lean Manufacturing
Lean manufacturing offre molti vantaggi alle aziende che la adottano. Uno dei principali vantaggi è l’aumento dell’efficienza, che porta a costi inferiori e maggiori profitti. Riducendo gli sprechi e semplificando i processi, le aziende possono produrre di più con meno, il che significa che possono abbassare i costi e offrire prezzi più competitivi ai clienti.
Un altro vantaggio della lean manufacturing è il miglioramento della qualità. Concentrandosi sull’eliminazione degli sprechi e sul miglioramento dei processi, le aziende possono identificare ed eliminare le cause alla radice dei difetti, ottenendo prodotti di qualità superiore. Ciò, a sua volta, porta a una maggiore soddisfazione e fedeltà dei clienti, poiché è più probabile che i clienti tornino a un’azienda che produce costantemente prodotti di alta qualità.
Lean manufacturing porta anche a una maggiore flessibilità e reattività. Riducendo i livelli di inventario e semplificando i processi, le aziende possono rispondere più rapidamente ai cambiamenti nella domanda dei clienti, il che può aiutarle a stare al passo con la concorrenza.
Implementazione della Lean manufacturing:
L’implementazione della Lean Manufacturing richiede un approccio sistematico che coinvolga tutti i livelli dell’organizzazione. Il primo passo è identificare e mappare i processi correnti, inclusi tutti gli input e gli output. Ciò contribuirà a identificare le aree in cui si verificano sprechi e dove è possibile apportare miglioramenti.
Una volta mappati i processi attuali, il passo successivo è analizzare i dati e identificare le cause profonde dei rifiuti. Ciò può comportare la raccolta di dati su tempi di ciclo, tassi di difetti e altri indicatori di prestazioni chiave.
Dopo aver identificato le cause profonde dei rifiuti, il passo successivo è sviluppare un piano per eliminarli. Ciò può comportare la reingegnerizzazione dei processi, la riprogettazione del prodotto o la riorganizzazione del layout dell’impianto di produzione.
Infine, è importante misurare il successo dell’implementazione della Lean manufacturing. Ciò si ottiene misurando gli indicatori chiave di prestazione (KPI) per valutare se gli obiettivi di efficienza, qualità e flessibilità sono stati raggiunti.
Cepicat e Lean manufacturing:
In conclusione, Lean manufacturing è una metodologia collaudata per migliorare l’efficienza, la qualità e la reattività delle aziende. Riducendo gli sprechi e semplificando i processi, le aziende possono produrre di più con meno, portando a costi inferiori e maggiori profitti. L’implementazione della Lean Manufacturing richiede un approccio sistematico che coinvolga tutti i livelli dell’organizzazione e la costante misurazione degli indicatori chiave di prestazione. Se implementata correttamente, lean manufacturing può aiutare le aziende a migliorare la propria competitività e stare al passo con la concorrenza.
Cepicat cerca sempre di progredire e migliorare, motivo per cui lean Manufacturing ha iniziato a essere applicata anni fa.